Mountable Head Cable Ties
- Material: Nylon 66 94v-2 certificated by UL.
- Usage: After bundling wires, fox them on plate with screw.
Mountable head cable ties are a versatile and practical solution for organizing and securing cables, wires, and hoses. These cable ties feature a unique head design that includes a mounting hole, allowing them to be securely fastened to a surface, providing a neat and permanent installation. They're commonly used in various industries, including automotive, telecommunications, and home improvement projects, where securing cables and maintaining an organized environment is essential.
Specifications
Item No. | Length |
Width (mm) |
Max Bundle Dia. E (mm) |
Min.loop Tensile Strength | ||
lnch | mm | LBS | KGS | |||
MH-2.5×100MH | 4″ | 100 | 2.5 | 22 | 18 | 8 |
MH-3.6×100MA | 4″ | 100 | 3.6 | 22 | 40 | 18 |
MH-3.6×150MH | 6″ | 150 | 3.6 | 32 | 40 | 22 |
MH-4.8×200MH | 8″ | 200 | 4.8 | 42 | 50 | 55 |
MH-7.2×300MH | 12″ | 300 | 7.2 | 80 | 120 | 55 |
MH-7.2×200MA | 8″ | 200 | 7.2 | 50 | 120 | 55 |
MH-7.2×350MA | 14″ | 350 | 7.2 | 90 | 120 | 55 |
MH-7.2×380MA | 14″ | 380 | 7.2 | 90 | 120 | 55 |
ACRHT stands out from numerous enterprises but can keep growing every year. The benefit is that they have a stable product manufacturing system. The injection molding machine from a domestic manufacturer by the ACRHT company is specially customized.
However, advanced equipment will not be enough to finish production. The 300 kg steel mold is the heart of the injection molding machine.
28 years ago, the boss of ACRHT began his business from mold processing. Determining the manufacturing capacity of a cable tie manufacturer at a high level can be known through its mold.
Undeniably, ACRHT company has an unusual ability in mold manufacturing. A set of cable tie molds joined by more than 10 independent pieces of patchwork, with the error of the entire mold data allowed within 30 microns.
To put these subtle errors dispersed among a dozen patchwork is an impossible task that the average age of less than 30 years old guys took on.
The preliminary processing of small parts can showcase their manufacturing process here. The molybdenum wire is a little thicker than the diameter of the hair, cutting the mold steel at 10 meters per second. In order to meet the requirements of small errors in the drawings, manual polishing is needed before sending it to the next procedure to complete the final shape for larger mold inserts.
ACRHT company has its effective weapon. Here is a room temperature space at about 22℃, a constant temperature space where the world's leading automation equipment provides the possibility for mold precision processing. The admissible error is only 3 microns here, smaller than one-tenth of a hair.
The last line of the mold processing program is here. Electrical spark discharge is instantaneous. The temperature goes above ten thousand degrees. High temperatures cause the local melting and corrosion of metals, allowing them to make the various needed shapes in the high hardness of mold steel.
This processing was first discovered and used in 1943 by former Soviet Union scientists. After years of improvement, the electrical spark process achieved accuracy that traditional machining finds difficult to achieve. Each mold insert, after finishing, will be assembled and finally checked here.
This processing was first discovered and used in 1943 by former Soviet Union scientists. After years of improvement, the electrical spark process achieved accuracy that traditional machining finds difficult to achieve. Each mold insert, after finishing, will be assembled and finally checked here.
Years ago, ACRHT's founder received directions from predecessors and continuously improved in the field of high quality.
This is the factory laboratory, ongoing product testing under extreme temperature environments, ranging from -40℃ to 55℃. Quality is easily assessed through the intuitive data.
Inquiry for Our Products
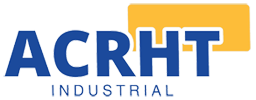
Email: info@acrht.com